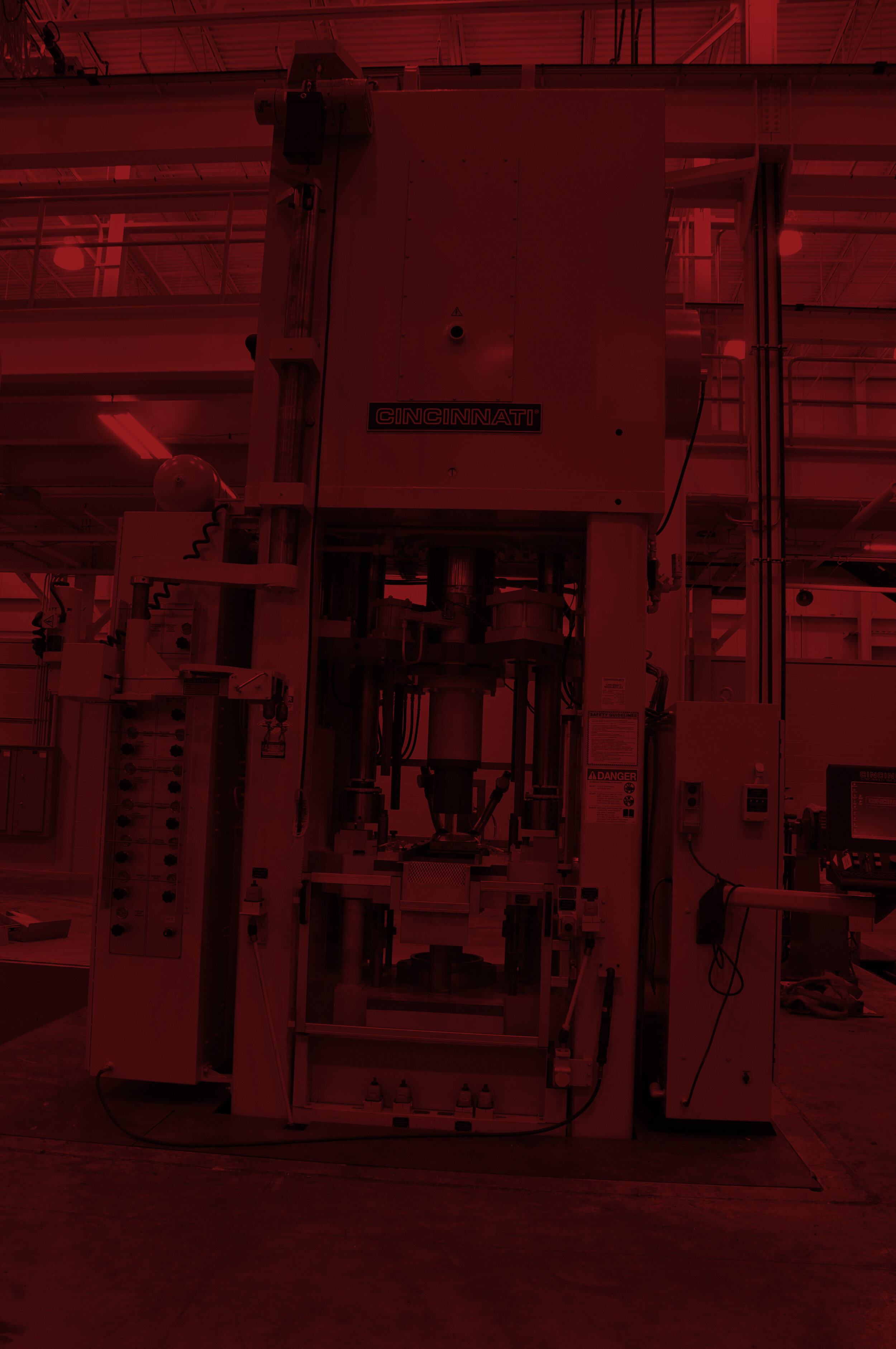
Rigid Reflex
Rigid Reflex Compacting Presses feature a rugged design perfectly suited for long run and high-speed production of a wide range of parts. These presses can produce parts up to 4 lower and 2 upper levels.
Rugged Precision Guiding
The main pressing ram is guided by a large diameter bearing and outboard guiding using long bearing husks running on the outboard guide rods. The platens are guided by long bearing husks running on large diameter guide rods that span from the crown to the bed of the press. This combination provides a rigid robust guiding system required to produce precision complex parts using close tooling tolerances.
CINCINNATI® follows the policy of continuous advancement in product development. For this reason, specifications and dimensions are for reference only and can change without notice. Foundation plans are furnished with each new machine installation.
Features | 220-C3-6 | 550-C3-4.5 | 825-C3-6 |
---|---|---|---|
Main Ram Pressing (tons) | 220 | 550 | 825 |
Productivity (SPM) | 10-30 | 6-18 | 5-15 |
# Of Pressing Levels Upper* | 3 | 3 | 3 |
# Of Pressing Levels Lower* | 4 | 4 | 4 |
Fill Depth (in) | 6 | 4.5 | 6 |
Die Opening (in) | 11-9/16 | 15-9/16 | 15-9/16 |
Platen Ejection Capacity (tons) | 100 | 200 | 200 |
Core Rod Ejection Capacity (tons) | 6 | 25 | 25 |
Feeder Opening (in) * | 6 | 9 | 9 |
Main Ram Tonnage Monitoring | ![]() |
![]() |
![]() |
Platen Motion Monitoring | ![]() |
![]() |
![]() |
Platen Tonnage Monitoring | ![]() |
![]() |
![]() |
SPC Data Collection | ![]() |
![]() |
![]() |
Main Ram Tonnage Monitor | ![]() |
![]() |
![]() |
Programmable Feeder | ![]() |
![]() |
![]() |
Powder Hopper(s) | ![]() |
![]() |
![]() |
Top Punch Holddown | ![]() |
![]() |
![]() |
Allen Bradley Control | ![]() |
![]() |
![]() |
Touchscreen HMI | ![]() |
![]() |
![]() |
Remote Diagnostics | ![]() |
![]() |
![]() |
Machine Commissioning & Training | ![]() |
![]() |
![]() |
*Options May be Required
Key Features
-
Mechanical Press
Mechanical presses are famous for their high production rates and part making accuracy. The all steel welded construction uses a tie rod design to provide a rigid robust press structure required for precision part production. An AC Variable Frequency main drive motor provides power to double reduction gearing contained in a fully enclosed crown located above the die area to keep powder out of critical drive mechanisms. All drive mechanisms are lubricated through a double filtered pressurized recirculation oil system to ensure long reliable service under demanding conditions.
-
Programmable Feeder System
CINCINNATI has been the leader in development of programmable controlled powder feeder systems. Operators have complete control over all critical powder feed shoe motions though the Press Control Center combined with an AC servo motor driven ball screw feeder drive. Good parts begin with consistent filling of the die cavity. The Parts Maker Programmable Feeder combination allows optimized part quality at the high production rates needed to be competitive now and in the future.
-
Withdrawal Press Motion
Withdrawal press motion permits start of the fill function earlier in the press cycle than other types of press motion. It also reduces potential for air entrapment and causes the least disruption of the powder during entry into the die cavity. This optimizes the press cycle and helps ensure production of high quality consistent parts.
-
Multi-Level Capability
With available options, Parts Maker Presses can be configured to produce multi-level parts using the following independently controlled part making tools: Inner Upper Punch, Middle Upper Punch, Outer Upper Punch, Shelf Die or Straight Die, Middle Platen Punch, Bottom Platen Punch, Stationary Punch, and Through, Stepped or Blind Core Rod
-
CINCINNATI Press Control Center
Fingertip programmable computer control of press functions is provided by the CINCINNATI CNC Compact Computer Control Center. The combination of Menu Driven Software and Softkey Technology simplify set-up and operation to reduce operator effort and ensure proper production of repeat production lots. Color graphics display operator oriented information to effectively highlight critical part making functions. This powerful control was specifically designed for CINCINNATI Powdered Metal presses and provides a full range of press control, monitoring and data collection features.
-
Extensive Support Services
CINCINNATI provides an extensive list of comprehensive support services with each new press to ensure many years of productive profitable service.