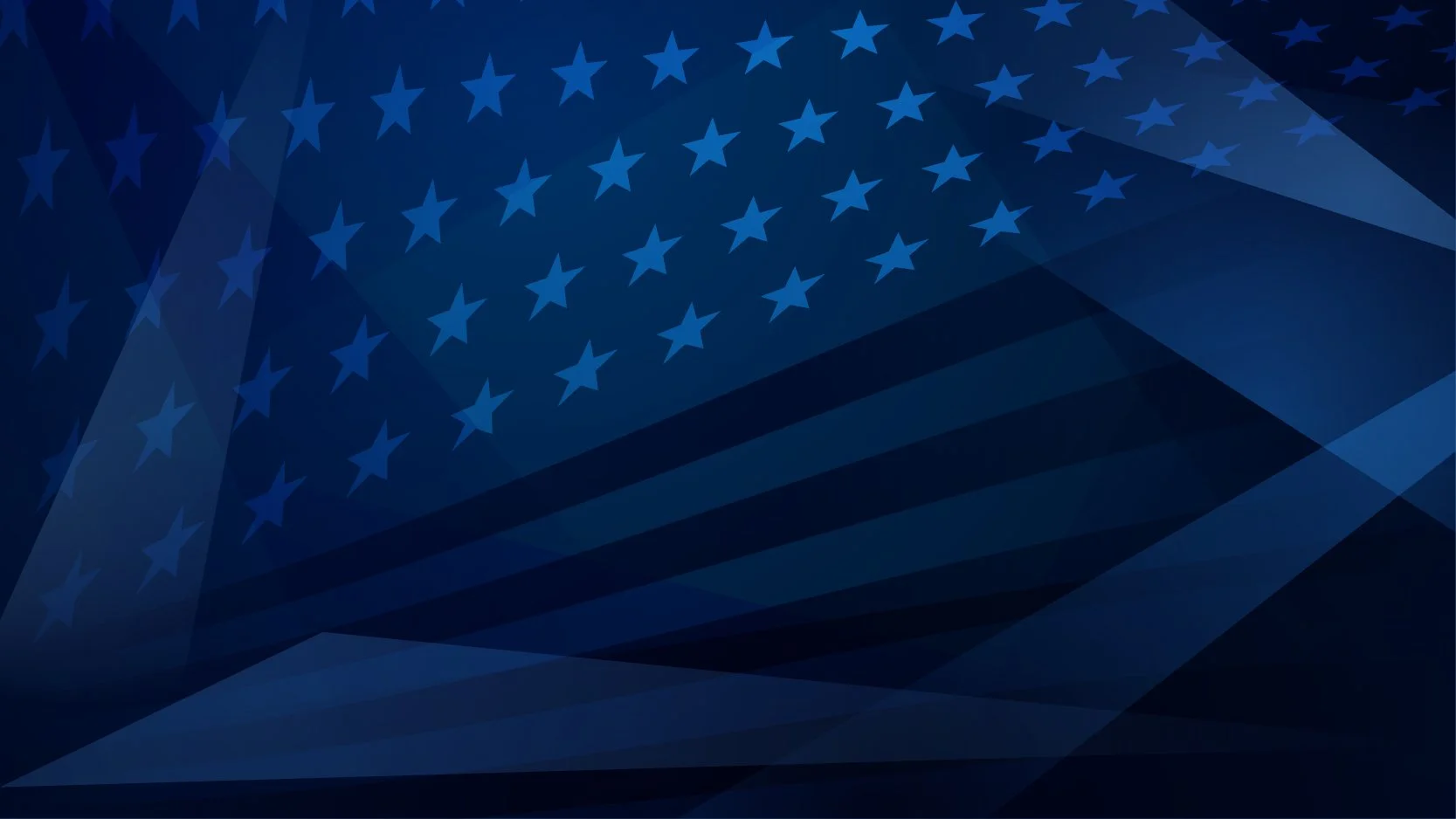
Celebrating our heroes and
releasing new Products all
in the same place!
September 8th - 11th | Booth A4567 | McCormick Place, Chicago IL
From simple to complex operations, we have the right equipment for you.
-
Fiber Lasers
Your key to cutting-edge performance and superior results
-
Automation
Designed to seamlessly integrate and optimize your workflow
-
Press Brakes
Innovative design results in exceptional forming control, constancy, and speed
-
Shears
Unbeatable precision and durability to ensure your fabrication work is always a cut above the rest
-
PM Presses
Unlock unparalleled efficiency and part quality
-
Software
Tackle projects with greater speed and quality
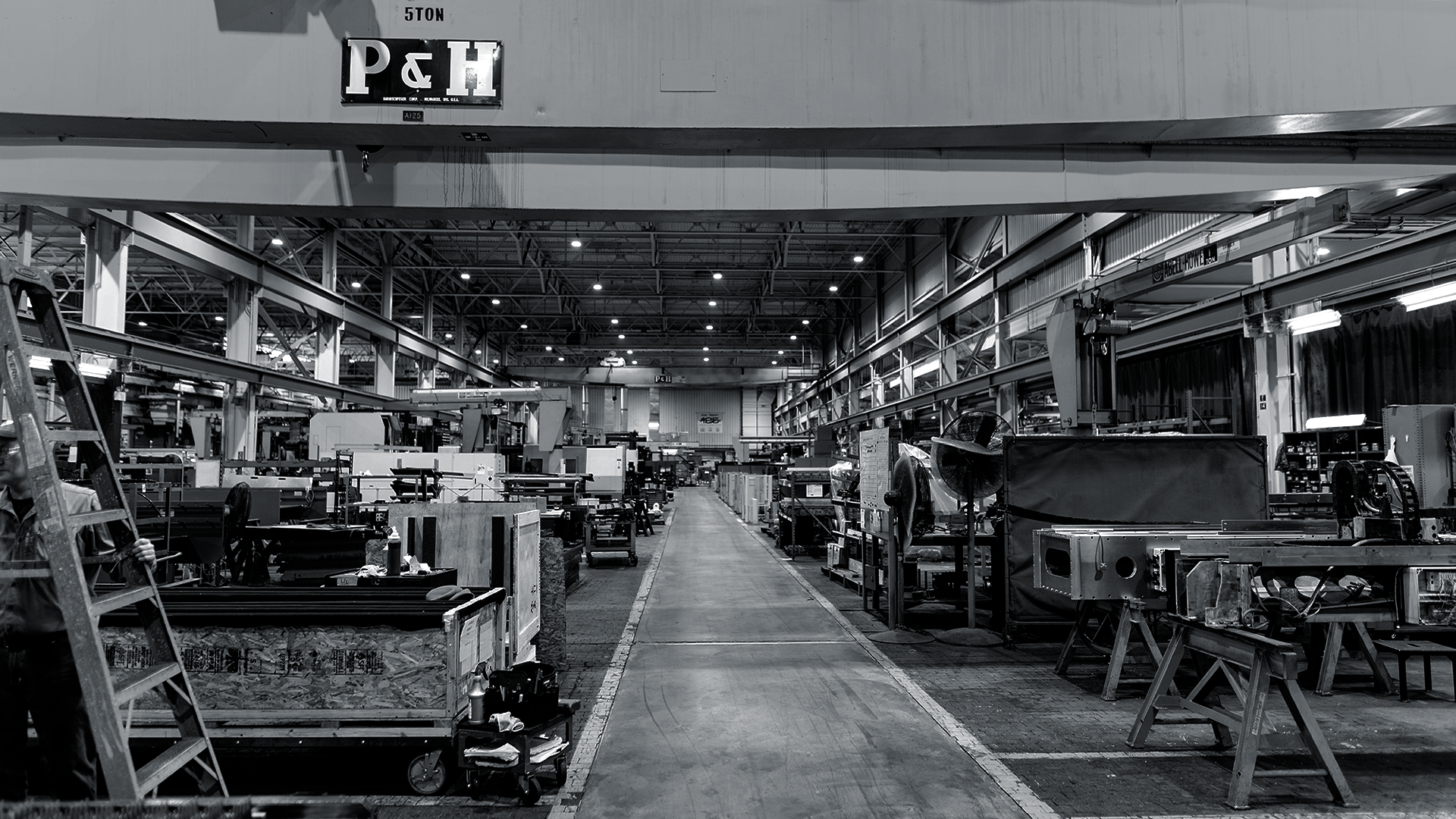
See why CI is a smart choice for fabricators
newsroom
Cincinnati Incorporated isn't just about the machines they build; it's about the passionate, skilled, and dedicated people who design, manufacture, sell, and support them. Their stories embody innovation, craftsmanship, and a commitment to excellence.
MOre Than Machines
Our engineers are ready to help!
Sponsorships
We believe in the power of partnership and the spirit of collaboration to spark innovation, nurture talent, and achieve greatness. That's why we're immensely proud to extend our support beyond the industrial boundaries, embracing the communities and passion points that resonate deeply with our values.
Legacy Meets Innovation
See Our Machines in Action
-
Harrison, OH
Get a personalized demonstration at Cincinnati Incorporated Headquarters.
-
Charlotte, NC
Visit the legendary Hendrick Motorsports campus and see our machine in action.
-
South El Monte, CA
Visit our friends at Sterling Machinery Exchange and see our wide array of press brake models.
Upcoming Events
#OwnIt
Follow Us on Social Media
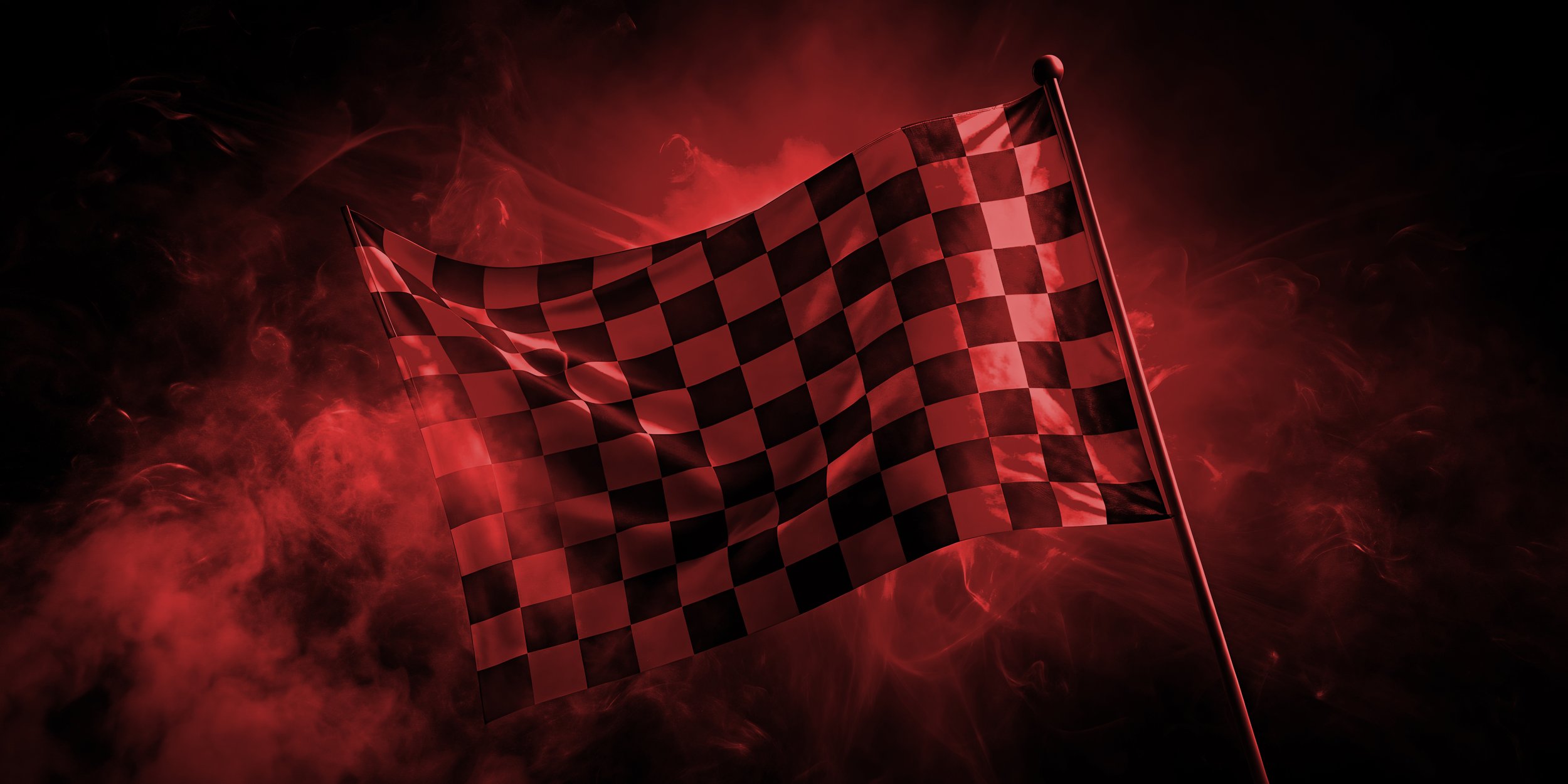
2025 Hendrick Motorsports Winner Circle
Winner of the Best Workplaces in Ohio Award
for 7 consecutive years!
2018
2024